Industry Insights: Optimizing Metal Fabrication Solutions
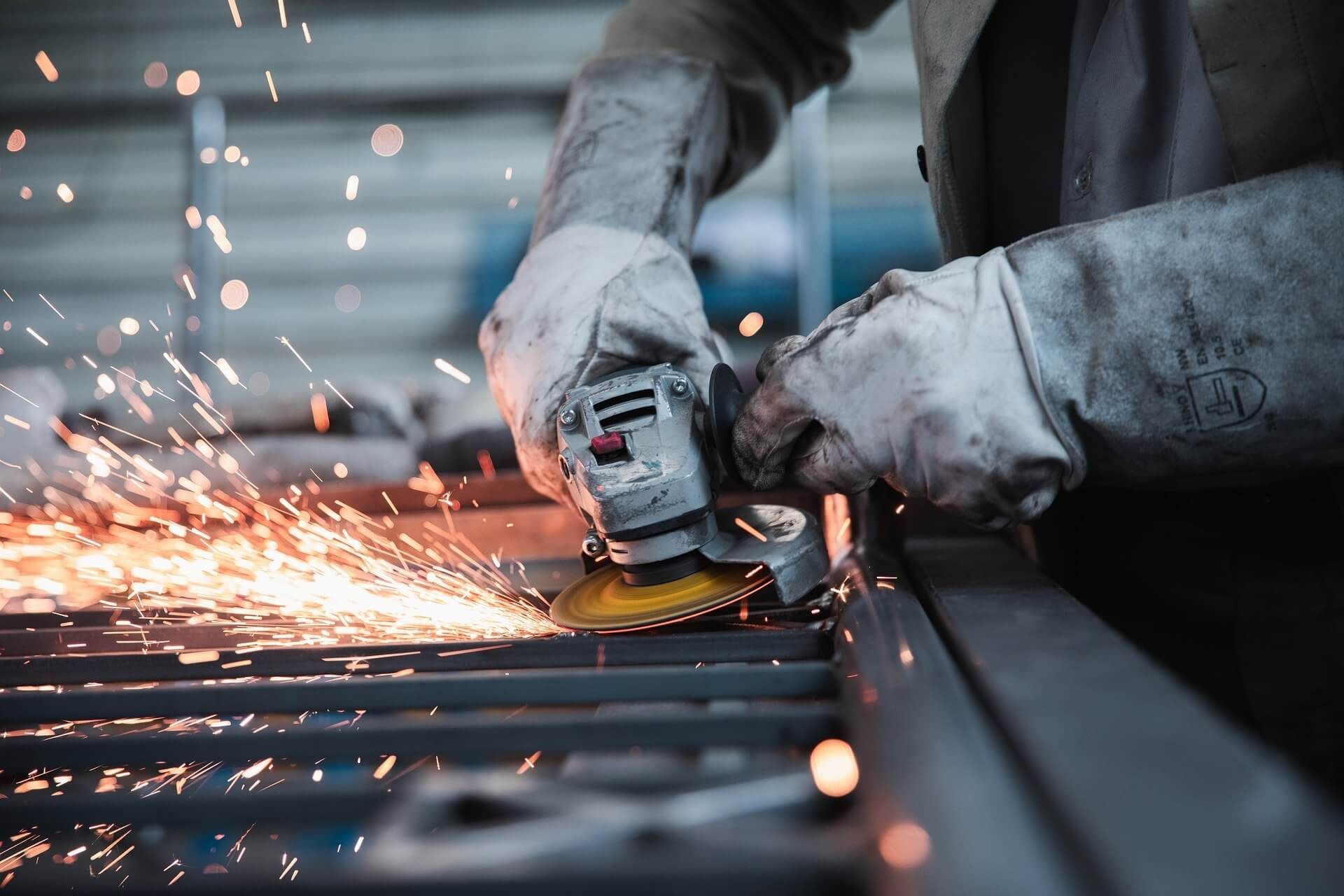
In today's fast-paced industrial landscape, metal fabrication has become the backbone of many industries, from construction and automotive to aerospace and heavy machinery. The demand for high-quality, efficient, and customized metal fabrication solutions is constantly increasing as companies seek to improve their production processes, minimize waste, and maximize profitability. But how can businesses optimize their metal fabrication operations to meet these challenges while maintaining quality and performance?
This blog post dives deep into the key strategies that industry leaders employ to optimize metal fabrication solutions, improve operational efficiency, and remain competitive in a market that demands excellence.
1. Automation: The Future of Metal Fabrication
Automation has revolutionized the manufacturing sector, and metal fabrication is no exception. Incorporating automated systems and robotics into the fabrication process can significantly reduce human error, speed up production times, and ensure greater precision. Automated laser cutting machines, for instance, provide faster and more accurate cuts compared to manual methods.
By automating tasks such as cutting, welding, and bending, fabricators can minimize downtime, enhance consistency, and reduce labor costs. Additionally, automation allows companies to scale their operations without the need for a significant increase in workforce, making it a scalable and cost-effective solution.
At Weldco Manufacturing, we leverage the latest automation technologies to deliver precision in every project. From advanced cutting equipment to state-of-the-art welding systems, our commitment to automation ensures that we meet the demands of modern industries with unparalleled accuracy and efficiency. Learn more about how we integrate automation into our services by visiting weldcomfg.com.
2. Embracing Lean Manufacturing Principles
Lean manufacturing principles focus on reducing waste and optimizing processes to increase efficiency. By identifying and eliminating non-value-added activities, businesses can streamline their operations and improve productivity. In metal fabrication, this could involve optimizing material usage, improving the flow of work processes, and reducing machine idle times.
One key aspect of lean manufacturing is just-in-time (JIT) production, which ensures that materials are only ordered and used as needed. This reduces excess inventory, minimizes waste, and frees up capital for other investments. Additionally, implementing a continuous improvement culture (also known as Kaizen) encourages employees to regularly assess and refine processes, leading to long-term efficiency gains.
At Weldco Manufacturing, lean manufacturing is at the heart of our operations. Our team continuously seeks ways to improve workflow, reduce waste, and increase efficiency without compromising quality. We pride ourselves on delivering high-performance, cost-effective solutions tailored to meet the unique needs of each client.
3. Material Optimization for Cost Savings and Durability
Choosing the right materials is critical to optimizing metal fabrication solutions. The material not only affects the cost of production but also influences the durability and performance of the final product. In today’s competitive market, balancing cost and quality is essential for businesses looking to maximize profitability without compromising product longevity.
One way to optimize material usage is through the application of lightweight alloys, which offer superior strength-to-weight ratios. These materials, such as aluminum or titanium alloys, are increasingly being used in industries like aerospace and automotive to reduce weight while maintaining structural integrity. Additionally, high-strength steel is another cost-effective alternative that can improve the durability of fabricated components without adding significant weight or cost.
Weldco Manufacturing specializes in selecting the best materials for each project, ensuring that clients receive cost-effective solutions without sacrificing performance. Our material experts work closely with clients to choose alloys and metals that meet their specific project requirements while optimizing for cost and durability. For more information on how we can help you choose the right materials for your next project, visit weldcomfg.com.
4. Investing in Workforce Training and Development
Even the most advanced machinery and optimized processes are only as effective as the people operating them. In metal fabrication, a skilled workforce is crucial to ensuring quality, efficiency, and safety. Investing in workforce training and development not only improves employee performance but also helps companies stay ahead of the curve with the latest industry trends and technologies.
By providing regular training sessions on new equipment, software, and fabrication techniques, companies can ensure that their workforce remains highly skilled and adaptable. Moreover, fostering a culture of continuous learning encourages innovation and problem-solving, which is essential for optimizing fabrication processes in an ever-evolving industry.
At Weldco Manufacturing, we believe that our people are our greatest asset. Our team is made up of highly skilled professionals who undergo continuous training to ensure that we stay at the forefront of industry advancements. From welding and machining to quality control and safety procedures, we invest in our workforce so that we can deliver the best possible solutions to our clients. Learn more about our team and our commitment to excellence at weldcomfg.com.
5. Implementing Advanced Software Solutions
In the digital age, advanced software tools have become essential in optimizing metal fabrication processes. Computer-aided design (CAD) software, for instance, allows for the precise planning and simulation of projects before production even begins. This reduces the likelihood of errors and ensures that fabricators can achieve optimal results on the first attempt.
Additionally, enterprise resource planning (ERP) systems can be used to integrate all aspects of the production process, from material procurement to final delivery. ERP software helps companies track inventory, monitor production schedules, and manage resources more efficiently, ensuring that projects are completed on time and within budget.
Weldco Manufacturing utilizes cutting-edge software solutions to streamline our operations and provide our clients with real-time project updates. From CAD design to ERP integration, our digital tools allow us to deliver high-quality fabrication solutions with unmatched efficiency. Discover how our software-driven approach can benefit your next project by
6. Prioritizing Sustainability and Environmental Responsibility
As industries worldwide shift toward more sustainable practices, metal fabrication companies must also prioritize environmental responsibility. By adopting eco-friendly manufacturing techniques, fabricators can reduce their carbon footprint, minimize waste, and improve their public image.
One key strategy is the implementation of recycling programs, where scrap metal is reused or repurposed instead of being discarded. Additionally, reducing energy consumption through more efficient machinery and production processes can further enhance a company’s sustainability efforts.
At Weldco Manufacturing, sustainability is a core value. We are committed to minimizing our environmental impact by implementing recycling programs and using energy-efficient equipment. Our goal is to not only provide high-quality fabrication solutions but also to contribute to a greener future. Find out more about our sustainability initiatives at weldcomfg.com.
7. Collaborative Partnerships for Customized Solutions
Every industry has unique metal fabrication requirements, whether it’s for custom parts, large-scale projects, or highly specialized components. Building strong partnerships with a trusted metal fabrication provider allows businesses to receive tailored solutions that meet their specific needs.
By working closely with clients, metal fabricators can provide customized design, material selection, and production processes that optimize efficiency and cost-effectiveness. This collaborative approach ensures that both parties are aligned on the project’s objectives, timelines, and budget, resulting in a successful outcome.
At Weldco Manufacturing, we pride ourselves on building lasting partnerships with our clients. Our collaborative approach ensures that we understand your unique challenges and can provide customized solutions that meet your exact specifications. Whether you need precision machining, welding, or large-scale fabrication, we’re here to help. To explore how we can work together, visit weldcomfg.com and get in touch with our team today.
Conclusion
Optimizing metal fabrication solutions requires a multifaceted approach that involves embracing automation, lean manufacturing principles, advanced software, and sustainability. By investing in these strategies, businesses can improve efficiency, reduce costs, and ensure the long-term success of their operations.
At Weldco Manufacturing, we are committed to delivering optimized metal fabrication solutions that meet the needs of modern industries. Whether you're looking to improve your production processes or need customized solutions for your next project, we have the expertise and technology to help you succeed. Visit weldcomfg.com to learn more about our services and how we can help you optimize your metal fabrication operations.