resources and articles
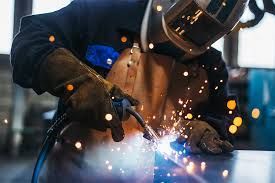
Metal fabrication has always been a cornerstone of industrial development, providing the backbone for countless industries from automotive to aerospace. As technology advances, so does the demand for more precise, efficient, and sustainable metal fabrication processes. In 2023, the metal fabrication industry is witnessing transformative trends that are not only shaping the present but also setting the course for future innovation. In this blog, we’ll explore the key trends in metal fabrication that are revolutionizing the industry this year and beyond. 1. Automation and Robotics: The Rise of the Smart Factory Automation is no longer just a buzzword; it's an integral part of the future of metal fabrication. With labor shortages, the need for greater efficiency, and the pressure to maintain competitive pricing, automation is stepping in to bridge the gap. Robots and automated systems are taking over repetitive tasks such as welding, cutting, and assembly, freeing up skilled labor for more complex jobs. Collaborative robots, also known as cobots, are designed to work alongside human operators. They improve productivity while maintaining flexibility, allowing manufacturers to scale operations without the need for massive workforce expansion. In 2023, we see a surge in factories implementing these smart technologies, leading to faster production times, fewer errors, and lower costs. What to Expect: The integration of artificial intelligence (AI) with automation systems is driving real-time decision-making and predictive maintenance. This reduces downtime and ensures that machinery operates at optimal efficiency. Companies that embrace this trend are more likely to stay ahead of the competition in terms of quality, precision, and speed. 2. Sustainability and Eco-Friendly Practices: A Green Revolution Sustainability is no longer optional; it's a necessity. The metal fabrication industry is under increasing pressure to reduce its carbon footprint and adopt eco-friendly practices. In 2023, more metal fabricators are turning to green manufacturing methods, including recycling scrap metal, using sustainable materials, and adopting energy-efficient production processes. The push for sustainability is also influencing the design of products. Lightweight materials that reduce energy consumption during transportation and use are becoming more popular, especially in industries like automotive and aerospace. Additionally, reducing waste and optimizing resource use have become key areas of focus for companies looking to stay competitive while minimizing their environmental impact. What to Expect: Sustainability in metal fabrication is driven by innovation. From the adoption of renewable energy sources in factories to the use of advanced software for waste reduction, the future of metal fabrication is green. Fabricators that implement these practices are likely to benefit from both cost savings and enhanced reputation, especially as consumer awareness around sustainability grows. 3. Additive Manufacturing: Beyond Prototyping Additive manufacturing, commonly known as 3D printing, is not new to metal fabrication, but in 2023 it is reaching new heights. While initially limited to prototyping, 3D printing has evolved into a technology capable of producing fully functional metal parts with complex geometries that traditional manufacturing methods cannot achieve. One of the significant advantages of additive manufacturing is its ability to produce parts on demand, reducing the need for large inventories and minimizing lead times. In industries where customization and small batch production are essential, such as aerospace and medical devices, additive manufacturing is proving to be a game-changer. What to Expect: As the technology becomes more advanced and accessible, we can expect to see even greater adoption of 3D printing in metal fabrication. The future lies in hybrid manufacturing processes that combine traditional methods with additive techniques, offering the best of both worlds in terms of speed, precision, and versatility. 4. Digitalization and Industry 4.0: Smart Metal Fabrication The rise of Industry 4.0 is revolutionizing how metal fabricators operate. By embracing digital technologies such as the Internet of Things (IoT), cloud computing, and advanced data analytics, manufacturers are creating smart factories that can monitor, control, and optimize every aspect of production in real time. In 2023, digital twins—virtual replicas of physical machines and processes—are being used to simulate and optimize production lines before making changes in the real world. This reduces downtime and ensures that equipment operates at peak efficiency. Additionally, advanced sensors embedded in machinery provide continuous feedback, enabling predictive maintenance that prevents costly breakdowns. What to Expect: The trend towards digitalization is set to continue, with more metal fabricators leveraging big data and AI to improve decision-making, reduce waste, and enhance product quality. Those who fail to adopt Industry 4.0 technologies risk falling behind their competitors. 5. Advanced Materials: Strength Meets Lightweight Design Material science is playing an increasingly important role in metal fabrication, especially as industries such as automotive, aerospace, and defense seek stronger yet lighter materials. In 2023, the demand for advanced materials, such as high-strength steel, aluminum alloys, and titanium, continues to grow. These materials offer exceptional durability and performance while reducing weight, which is crucial for fuel efficiency and sustainability. Metal fabricators are also exploring new composite materials that combine metal with other substances, such as carbon fiber, to create components that are not only strong and lightweight but also resistant to corrosion and wear. What to Expect: The development of new materials will continue to drive innovation in metal fabrication. As industries push for greater performance and sustainability, fabricators must stay up to date with the latest advancements in material science to meet these evolving demands. 6. Cybersecurity: Protecting the Future of Metal Fabrication As metal fabrication becomes more digital and connected, the need for robust cybersecurity measures is greater than ever. Smart factories that rely on IoT devices, cloud-based systems, and data analytics are vulnerable to cyberattacks. In 2023, cybersecurity is a top concern for metal fabricators looking to protect their sensitive information, intellectual property, and operational systems. Cybersecurity threats can result in production downtime, data breaches, and financial losses. Therefore, metal fabricators are increasingly investing in secure networks, encrypted communications, and advanced firewalls to safeguard their operations. What to Expect: Cybersecurity will remain a critical focus for metal fabricators as they adopt more digital technologies. Companies that prioritize cybersecurity can prevent costly disruptions and ensure the integrity of their operations. 7. Customization and On-Demand Manufacturing In an era where customers demand personalized products, metal fabricators are adapting by offering more customization options and on-demand manufacturing services. Thanks to advancements in software and machinery, fabricators can now produce bespoke metal components in small batches with minimal setup time. This trend is particularly relevant in industries like consumer electronics, medical devices, and automotive, where customization can set a company apart from its competitors. In 2023, metal fabricators are focusing on flexibility and responsiveness, allowing them to meet the unique needs of their clients without sacrificing efficiency. What to Expect: Customization will continue to be a driving force in metal fabrication. As consumer expectations evolve, metal fabricators must stay agile, offering tailored solutions that cater to the individual needs of their clients. Conclusion The metal fabrication industry is at the forefront of innovation, with 2023 ushering in transformative trends that will shape its future. From automation and sustainability to advanced materials and digitalization, metal fabricators are embracing new technologies and practices that improve efficiency, reduce costs, and enhance product quality. Companies that stay ahead of these trends will be better equipped to meet the evolving demands of their clients and remain competitive in the global market. At Weldco Manufacturing , we are committed to staying at the cutting edge of the metal fabrication industry. Our team of experts is dedicated to delivering high-quality, precision-engineered metal products that meet the unique needs of our clients. Whether you need custom metal fabrication, advanced materials, or sustainable manufacturing solutions, we’ve got you covered. Visit weldcomfg .com to learn more about our services and how we can help shape your future.
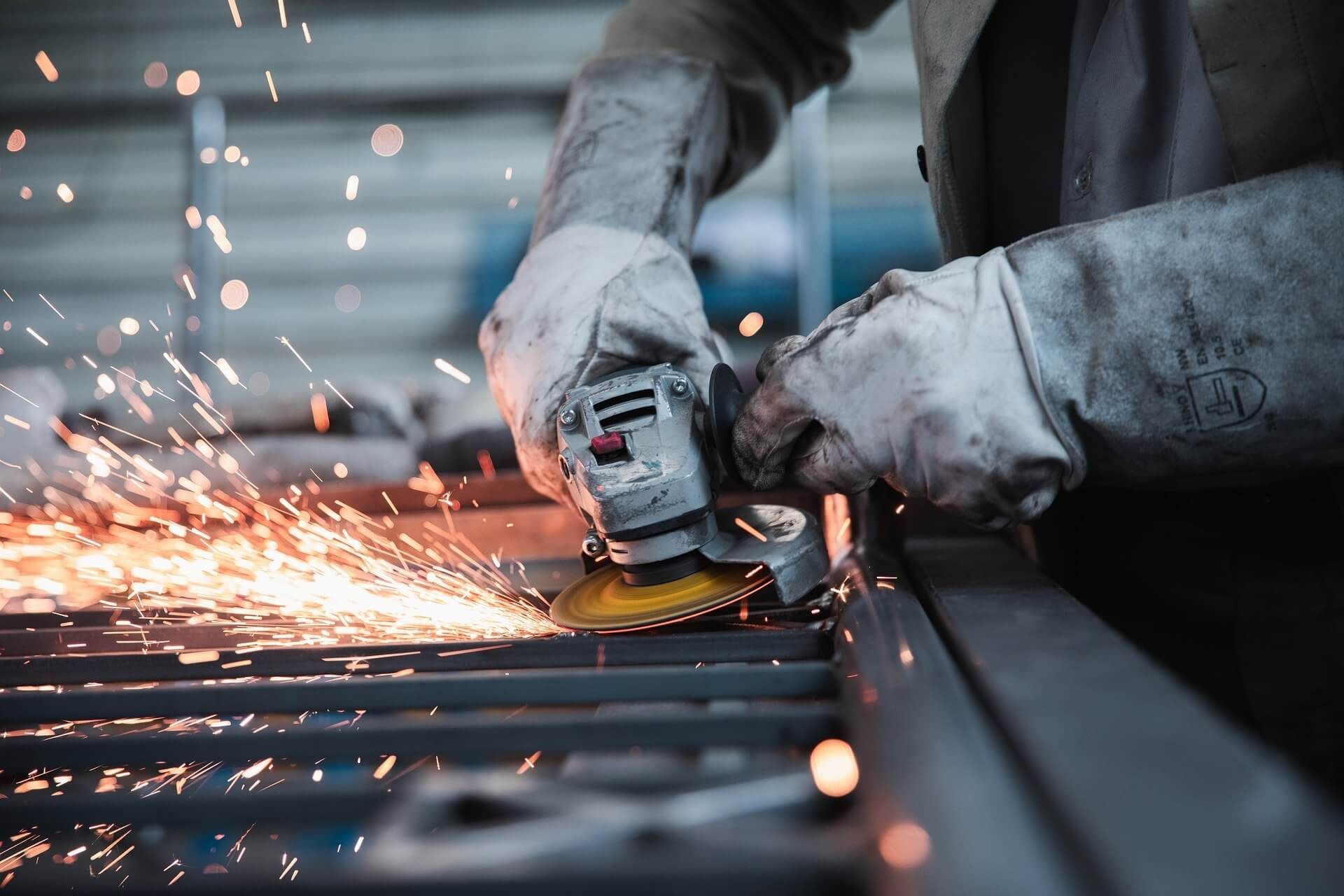
In today's fast-paced industrial landscape, metal fabrication has become the backbone of many industries, from construction and automotive to aerospace and heavy machinery. The demand for high-quality, efficient, and customized metal fabrication solutions is constantly increasing as companies seek to improve their production processes, minimize waste, and maximize profitability. But how can businesses optimize their metal fabrication operations to meet these challenges while maintaining quality and performance? This blog post dives deep into the key strategies that industry leaders employ to optimize metal fabrication solutions, improve operational efficiency, and remain competitive in a market that demands excellence. 1. Automation: The Future of Metal Fabrication Automation has revolutionized the manufacturing sector, and metal fabrication is no exception. Incorporating automated systems and robotics into the fabrication process can significantly reduce human error, speed up production times, and ensure greater precision. Automated laser cutting machines, for instance, provide faster and more accurate cuts compared to manual methods. By automating tasks such as cutting, welding, and bending, fabricators can minimize downtime, enhance consistency, and reduce labor costs. Additionally, automation allows companies to scale their operations without the need for a significant increase in workforce, making it a scalable and cost-effective solution. At Weldco Manufacturing , we leverage the latest automation technologies to deliver precision in every project. From advanced cutting equipment to state-of-the-art welding systems, our commitment to automation ensures that we meet the demands of modern industries with unparalleled accuracy and efficiency. Learn more about how we integrate automation into our services by visiting weldco mfg. com . 2. Embracing Lean Manufacturing Principles Lean manufacturing principles focus on reducing waste and optimizing processes to increase efficiency. By identifying and eliminating non-value-added activities, businesses can streamline their operations and improve productivity. In metal fabrication, this could involve optimizing material usage, improving the flow of work processes, and reducing machine idle times. One key aspect of lean manufacturing is just-in-time (JIT) production, which ensures that materials are only ordered and used as needed. This reduces excess inventory, minimizes waste, and frees up capital for other investments. Additionally, implementing a continuous improvement culture (also known as Kaizen ) encourages employees to regularly assess and refine processes, leading to long-term efficiency gains. At Weldco Manufacturing, lean manufacturing is at the heart of our operations. Our team continuously seeks ways to improve workflow, reduce waste, and increase efficiency without compromising quality. We pride ourselves on delivering high-performance, cost-effective solutions tailored to meet the unique needs of each client. 3. Material Optimization for Cost Savings and Durability Choosing the right materials is critical to optimizing metal fabrication solutions. The material not only affects the cost of production but also influences the durability and performance of the final product. In today’s competitive market, balancing cost and quality is essential for businesses looking to maximize profitability without compromising product longevity. One way to optimize material usage is through the application of lightweight alloys , which offer superior strength-to-weight ratios. These materials, such as aluminum or titanium alloys, are increasingly being used in industries like aerospace and automotive to reduce weight while maintaining structural integrity. Additionally, high-strength steel is another cost-effective alternative that can improve the durability of fabricated components without adding significant weight or cost. Weldco Manufacturing specializes in selecting the best materials for each project, ensuring that clients receive cost-effective solutions without sacrificing performance. Our material experts work closely with clients to choose alloys and metals that meet their specific project requirements while optimizing for cost and durability. For more information on how we can help you choose the right materials for your next project, visit weldc omfg.com. 4. Investing in Workforce Training and Development Even the most advanced machinery and optimized processes are only as effective as the people operating them. In metal fabrication, a skilled workforce is crucial to ensuring quality, efficiency, and safety. Investing in workforce training and development not only improves employee performance but also helps companies stay ahead of the curve with the latest industry trends and technologies. By providing regular training sessions on new equipment, software, and fabrication techniques, companies can ensure that their workforce remains highly skilled and adaptable. Moreover, fostering a culture of continuous learning encourages innovation and problem-solving, which is essential for optimizing fabrication processes in an ever-evolving industry. At Weldco Manufacturing, we believe that our people are our greatest asset. Our team is made up of highly skilled professionals who undergo continuous training to ensure that we stay at the forefront of industry advancements. From welding and machining to quality control and safety procedures, we invest in our workforce so that we can deliver the best possible solutions to our clients. Learn more about our team and our commitment to excellence at weldco mfg.c om . 5. Implementing Advanced Software Solutions In the digital age, advanced software tools have become essential in optimizing metal fabrication processes. Computer-aided design (CAD) software, for instance, allows for the precise planning and simulation of projects before production even begins. This reduces the likelihood of errors and ensures that fabricators can achieve optimal results on the first attempt. Additionally, enterprise resource planning (ERP) systems can be used to integrate all aspects of the production process, from material procurement to final delivery. ERP software helps companies track inventory, monitor production schedules, and manage resources more efficiently, ensuring that projects are completed on time and within budget. Weldco Manufacturing utilizes cutting-edge software solutions to streamline our operations and provide our clients with real-time project updates. From CAD design to ERP integration, our digital tools allow us to deliver high-quality fabrication solutions with unmatched efficiency. Discover how our software-driven approach can benefit your next project by visiting weldcom fg.com. 6. Prioritizing Sustainability and Environmental Responsibility As industries worldwide shift toward more sustainable practices, metal fabrication companies must also prioritize environmental responsibility. By adopting eco-friendly manufacturing techniques , fabricators can reduce their carbon footprint, minimize waste, and improve their public image. One key strategy is the implementation of recycling programs , where scrap metal is reused or repurposed instead of being discarded. Additionally, reducing energy consumption through more efficient machinery and production processes can further enhance a company’s sustainability efforts. At Weldco Manufacturing, sustainability is a core value. We are committed to minimizing our environmental impact by implementing recycling programs and using energy-efficient equipment. Our goal is to not only provide high-quality fabrication solutions but also to contribute to a greener future. Find out more about our sustainability initiatives at w eldcomfg.com. 7. Collaborative Partnerships for Customized Solutions Every industry has unique metal fabrication requirements, whether it’s for custom parts, large-scale projects, or highly specialized components. Building strong partnerships with a trusted metal fabrication provider allows businesses to receive tailored solutions that meet their specific needs. By working closely with clients, metal fabricators can provide customized design, material selection, and production processes that optimize efficiency and cost-effectiveness. This collaborative approach ensures that both parties are aligned on the project’s objectives, timelines, and budget, resulting in a successful outcome. At Weldco Manufacturing, we pride ourselves on building lasting partnerships with our clients. Our collaborative approach ensures that we understand your unique challenges and can provide customized solutions that meet your exact specifications. Whether you need precision machining, welding, or large-scale fabrication, we’re here to help. To explore how we can work together, visit weldcomfg.com and get in touch with our team today. Conclusion Optimizing metal fabrication solutions requires a multifaceted approach that involves embracing automation, lean manufacturing principles, advanced software, and sustainability. By investing in these strategies, businesses can improve efficiency, reduce costs, and ensure the long-term success of their operations. At Weldco Manufacturing, we are committed to delivering optimized metal fabrication solutions that meet the needs of modern industries. Whether you're looking to improve your production processes or need customized solutions for your next project, we have the expertise and technology to help you succeed. Visit weldcomfg.com to learn more about our services and how we can help you optimize your metal fabrication operations.
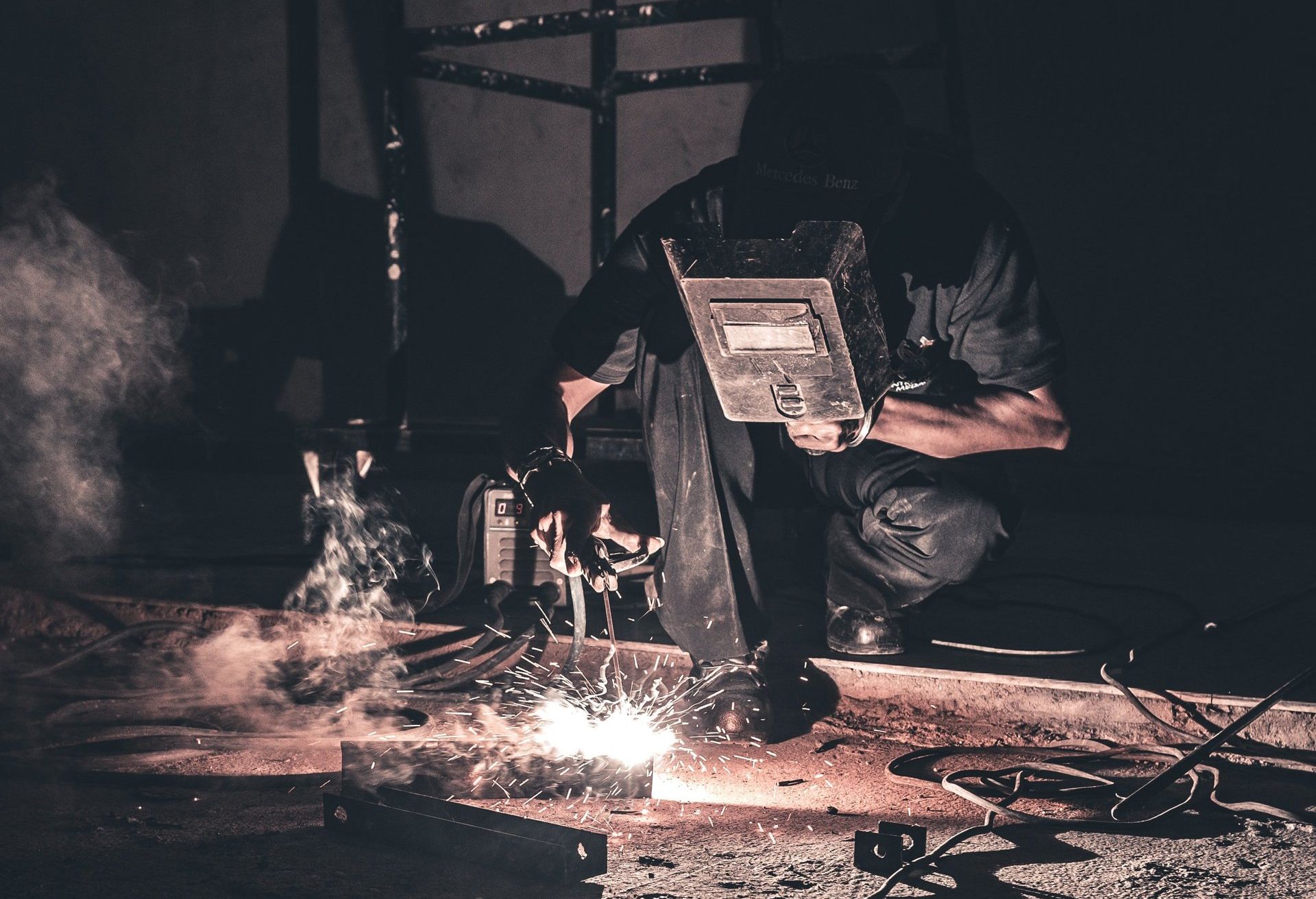
In the realm of metal fabrication and industrial construction, welding stands as one of the most critical processes. It is the art and science of fusing materials together, creating structures and components that are vital to various industries, from automotive to aerospace, construction to manufacturing. At Weldco Manufacturing, we take immense pride in our team of certified welders who embody the pinnacle of craftsmanship and expertise in this essential field. The Significance of Certified Welders Welding is not merely about joining two pieces of metal. It requires a deep understanding of metallurgy, precision, and skill. Certified welders at Weldco Manufacturing undergo rigorous training and certification processes to ensure they meet the highest industry standards. This certification is more than just a credential; it is a testament to their proficiency, dedication, and commitment to quality. The Certification Journey The journey to becoming a certified welder at Weldco Manufacturing is both challenging and rewarding. It begins with comprehensive education and training in various welding techniques, including MIG (Metal Inert Gas), TIG (Tungsten Inert Gas), and Stick welding. These techniques require different skills and are used for different applications, each with its own set of intricacies. 1. Classroom Instruction: The initial phase involves classroom instruction where aspiring welders learn the theoretical aspects of welding. This includes understanding welding symbols, blueprints, and the science behind different metals and their properties. They are taught how to identify potential issues that could compromise the integrity of a weld. 2. Hands-On Training: Following the classroom instruction, the trainees move to hands-on training. This phase is crucial as it allows them to apply their theoretical knowledge in a controlled environment. Under the guidance of experienced instructors, they practice welding techniques, focusing on precision, consistency, and safety. 3. Rigorous Testing: Certification requires passing a series of tests that evaluate both theoretical knowledge and practical skills. These tests are designed to simulate real-world scenarios, challenging the welders to demonstrate their ability to perform under pressure while adhering to strict quality standards. Mastering the Craft At Weldco Manufacturing, certified welders are not just technicians; they are artisans. Their work involves a meticulous process that ensures every weld is perfect, contributing to the durability and reliability of the final product. 1. Preparation: The welding process begins long before the first spark flies. Proper preparation is crucial to achieving a strong, clean weld. This includes cleaning the metal surfaces, setting up the work area, and ensuring all tools and equipment are in optimal condition. Our welders meticulously inspect each component, identifying any potential issues that need to be addressed before welding begins. 2. Precision Welding: Once everything is prepared, the actual welding process begins. Our certified welders employ a range of techniques, depending on the specific requirements of the project. They understand that different materials and applications demand different approaches. For instance, welding aluminum requires a different technique compared to stainless steel. The ability to adapt and apply the appropriate method is what sets our welders apart. 3. Quality Control: After the welding is completed, rigorous quality control checks are conducted. This involves visual inspections, non-destructive testing (NDT), and other methods to ensure the integrity of the weld. Any defects, no matter how minor, are addressed immediately to maintain the highest standards of quality. Innovation and Continuous Improvement The field of welding is constantly evolving, with new technologies and techniques emerging regularly. At Weldco Manufacturing, we believe in continuous improvement and innovation. Our certified welders are encouraged to stay updated with the latest advancements in welding technology. Regular training sessions and workshops are conducted to enhance their skills and knowledge. 1. Advanced Equipment: We invest in state-of-the-art welding equipment and tools that enhance precision and efficiency. This not only improves the quality of our work but also ensures the safety of our welders. Advanced equipment allows for more accurate control of the welding process, resulting in stronger and more reliable welds. 2. Research and Development: Our commitment to excellence drives us to continuously explore new materials and methods. Our research and development team works closely with our welders to test and implement innovative solutions that improve the welding process. This collaborative approach ensures that we remain at the forefront of the industry. The Importance of Safety Welding is inherently dangerous, involving high temperatures, intense light, and hazardous fumes. At Weldco Manufacturing, the safety of our welders is paramount. We adhere to strict safety protocols and provide our welders with the necessary protective gear and equipment. 1. Protective Gear: Our welders are equipped with high-quality protective gear, including welding helmets, gloves, and flame-resistant clothing. This gear is designed to protect them from burns, UV radiation, and harmful fumes. 2. Safety Training: Regular safety training sessions are conducted to ensure our welders are aware of the latest safety practices and regulations. They are trained to recognize potential hazards and take the necessary precautions to prevent accidents. The Final Product The result of this meticulous process is a final product that exemplifies quality and durability. Whether it’s a complex structural component for a skyscraper or a precision part for an aircraft, our welders’ craftsmanship ensures that every weld is flawless. This dedication to excellence is what makes Weldco Manufacturing a trusted name in the industry. A Commitment to Excellence At Weldco Manufacturing, we are committed to delivering the highest quality products to our clients. Our certified welders play a crucial role in this commitment, bringing their expertise, precision, and dedication to every project. We understand that our clients rely on us for products that are not only functional but also reliable and durable. This is why we invest in the best talent, training, and equipment. Join Us in Crafting Excellence If you’re looking for a partner who values quality and excellence as much as you do, look no further than Weldco Manufacturing. Our team of certified welders is ready to bring their expertise to your next project. Visit our website at Weldco Manufacturing to learn more about our services and how we can help you achieve your goals. Join us in crafting excellence, one weld at a time.
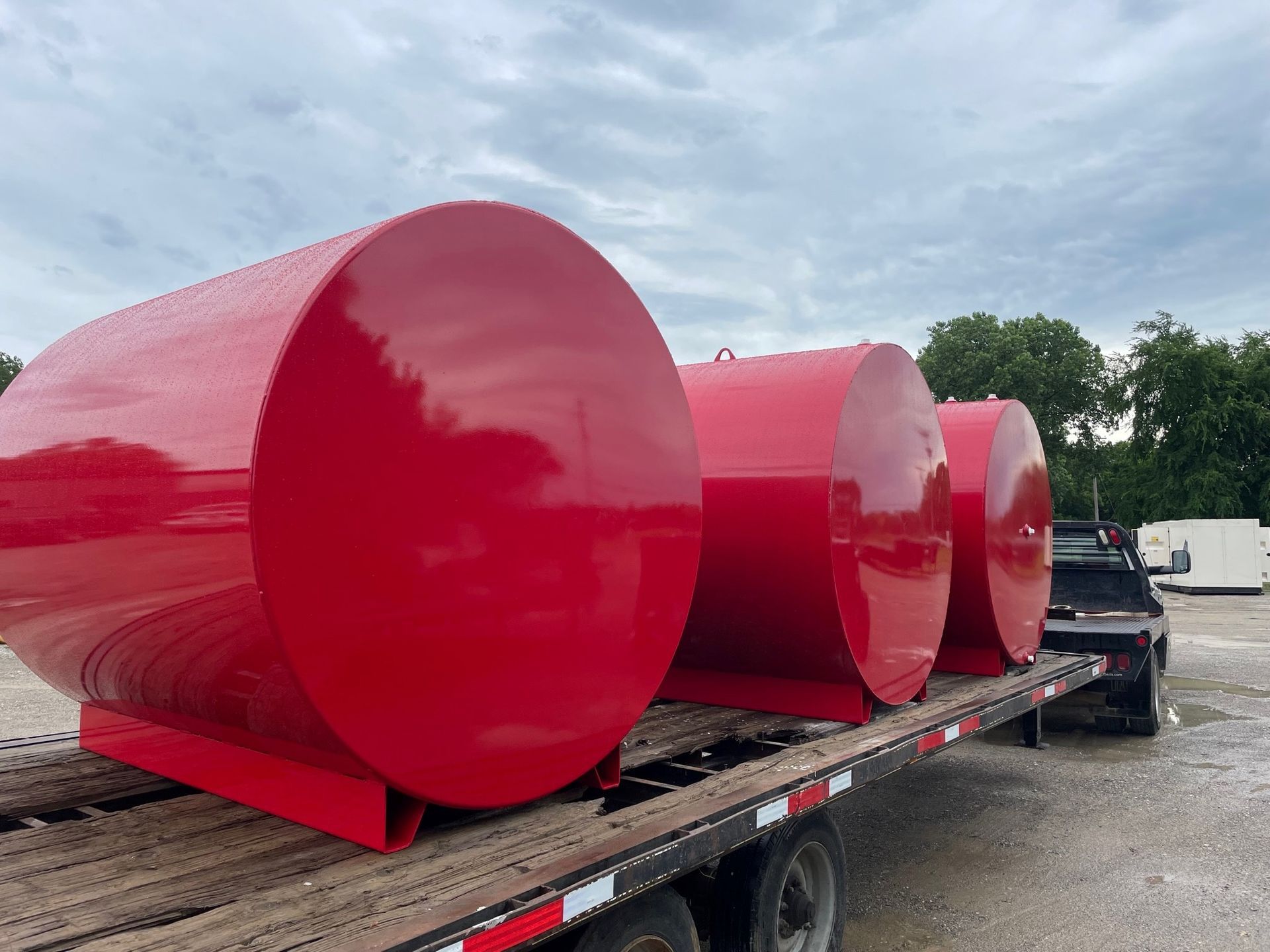
Above ground storage tanks (ASTs) are containers used to store various substances, such as fuel, chemicals, and water, above the ground surface. They are often found in industries such as oil and gas, chemical manufacturing, agriculture, and transportation, providing a cost-effective and convenient solution for storing large volumes of these substances.The importance of these tanks in these industries cannot be overstated as they play a vital role in the operations of such sectors. The article discusses a 290 gallon steel AST used for storing and dispensing gasoline. The integrity and design of these tanks are critical as they hold substances that could pose a risk if not stored correctly. Therefore, selecting the right type of tank is paramount to ensure compliance with regulations and meet specific operational needs. There are several types of ASTs, but in this article, we will zero in on two main types: single wall and double wall tanks . We will explore the differences between these two, their advantages, safety considerations, and how they comply with regulations. Additionally, it is important to note that ASTs are subject to stringent regulations and guidelines to ensure the safe storage and handling of hazardous materials. These regulations are put in place by environmental and safety bodies to protect the environment and the people working around these tanks. Compliance with these regulations is not just a legal requirement, but it's also an ethical obligation to safeguard our environment. Single Wall Tanks: An Overview Single wall tanks, as the name suggests, consist of a single layer of metal that directly holds the stored substance.This design is straightforward and effective, fulfilling the basic requirement of a storage tank , which is to safely contain substances.Single wall tanks are commonly used in situations where [secondary containment](http://www.epacinc.com/single-wall-vs-double-wall-fuel-tanks-need) , such as a concrete structure coated with epoxy, is already in place to prevent leaks. Single wall tanks offer several benefits, including affordability and flexibility in placement. One specific type of single wall tank worth mentioning is the diked tank. Diked tanks are a subtype of single wall tanks that come with an integral steel containment structure in the form of an open-top dike. This design provides secondary containment in the event of a leak, thereby minimizing the risk of environmental contamination. This is an excellent example of how the single wall tank design can be augmented to increase safety. While single wall tanks are often used when there is an existing concrete structure available for containment, it should be noted that this structure must meet specific requirements to be considered effective. This concrete structure needs to be coated with a substance such as epoxy to prevent the corrosive action of the stored substances. Besides, it should be inspected regularly for any signs of wear or damage that could compromise its effectiveness. This underscores the need for additional safety measures when dealing with single wall tanks. Double Wall Tanks: An Overview Double wall tanks take safety and environmental protection a notch higher with their innovative design. Unlike their single-wall counterparts, double wall tanks are designed with two layers of metal, with the primary tank surrounded by a secondary containment layer. This design essentially provides a tank within a tank, significantly increasing the level of safety and protection against leaks. The secondary containment layer in double wall tanks offers an extra level of protection. Should there be a leak in the primary tank, the secondary containment layer is ready to catch the leaked substance before it can enter the environment, offering a fail-safe mechanism. This is especially crucial when storing substances that are potentially harmful to the environment or pose a fire risk. An important feature of double wall tanks is their monitoring systems. These systems are designed to detect leaks and prevent rainwater from entering the tank, further enhancing the safety and efficiency of these tanks. For instance, a vacuum gauge is often installed between the two walls to monitor the space. Any change in the vacuum level could indicate a leak, prompting immediate action. Double wall tanks also offer resistance to inclement weather conditions. Their robust construction can withstand high winds and heavy rainfall, ensuring that the stored substance remains safe even in harsh weather conditions. This is a critical feature as exposure to adverse weather conditions could cause damage to the tank and potentially lead to leaks. Comparison: Single Wall vs Double Wall Tanks When comparing single wall and double wall tanks, several factors should be taken into account. These factors include cost, space and existing structures, compliance with regulations, placement and flexibility, leak monitoring systems, and resistance to weather conditions. When it comes to cost, single wall tanks generally have a lower initial cost than double wall tanks. This can make them an attractive option for businesses operating on a tight budget. However, it's important to note that while single wall tanks may have a lower upfront cost, additional expenses may be incurred for secondary containment systems, such as concrete structures or other approved methods [3, 4]. Space and existing structures also play a key role in the decision-making process. While single wall tanks require additional concrete structures for containment, double wall tanks do not. This can make double wall tanks a more convenient option in situations where space is limited or there is no existing containment structure [3, 4]. Compliance with Environmental Protection Agency (EPA) regulations is a crucial consideration in the choice between single wall and double wall tanks. Double wall tanks automatically comply with EPA regulations due to their built-in secondary containment . In contrast, single wall tanks may require additional measures, such as secondary containment systems, to achieve compliance [3, 4]. When it comes to placement and flexibility, single wall tanks offer more flexibility, especially if there is an existing concrete structure available. However, double wall tanks, with their built-in secondary containment, may not require specific placement to ensure containment. Leak monitoring is another important factor in the comparison. Double wall tanks have built-in leak monitoring systems, providing an added layer of protection and peace of mind. Single wall tanks, on the other hand, may require additional leak detection systems to ensure safety. Finally, weather resistance can be a key factor, especially in areas prone to severe weather conditions. Double wall tanks offer resistance to inclement weather conditions, ensuring the stored substance remains safe. In summary, when choosing between single wall and double wall tanks, it's crucial to consider all these factors. The decision should be based on a thorough assessment of the specific needs, budget, and regulatory requirements of the operation. Safety Considerations for Above Ground Storage Tanks When it comes to above ground storage tanks , safety is paramount. For single wall tanks, the absence of a built-in secondary containment means it is critical to have an effective secondary containment measure in place, such as a concrete structure coated with epoxy. This is to ensure that in the event of a leak, the leaked substance is contained and does not seep into the environment. Additionally, regular inspections of the tank and the secondary containment structure are crucial to ensure their integrity. This is particularly important for single wall tanks where the risk of leaked substances reaching the environment is higher due to the absence of a built-in secondary containment. Regular inspections can help detect any signs of wear or damage early, allowing for timely repairs and prevention of potential leaks. Double wall tanks, on the other hand, have an inherent secondary containment system. This design is a significant safety feature as it provides a built-in safeguard against leaks. However, this does not eliminate the need for regular inspections and maintenance. The secondary containment layer should be routinely inspected to ensure its integrity and functionality. Furthermore, double wall tanks often come equipped with leak monitoring systems. These systems provide an added layer of safety by detecting leaks early, allowing for prompt action to prevent environmental damage. Regular testing and calibration of these systems are necessary to ensure they remain effective in detecting leaks. In summary, regardless of the type of tank, adherence to safety guidelines and regulations is crucial in ensuring the safe storage and handling of substances. Regular inspections, routine maintenance, and effective leak detection and containment measures are key in ensuring the safety of above ground storage tanks. Importance of EPA Compliance and Regulations Compliance with Environmental Protection Agency (EPA) regulations is a critical aspect of operating above ground storage tanks. The EPA has specific guidelines and requirements in place to ensure the safe storage and handling of hazardous substances.These regulations are designed to protect the environment from potential contamination that can result from leaks or spills. Double wall tanks are designed to automatically meet these EPA regulations. Their built-in secondary containment provides an added layer of protection, minimizing the risk of leaks and environmental contamination. This makes double wall tanks an attractive option for businesses looking to ensure regulatory compliance with minimal additional measures [3, 4, 5]. Single wall tanks, on the other hand, may require additional measures to achieve compliance with EPA regulations. This could include the installation of secondary containment systems or other approved methods to prevent leaks [3, 4]. It is essential to understand these requirements and ensure that they are met when choosing and operating single wall tanks. In addition to federal regulations, state and local regulations may also apply to above ground storage tanks. These can vary from one location to another and may have specific requirements regarding tank design, installation, operation, and maintenance. It is essential to understand these regulations and ensure compliance to avoid penalties and ensure environmental protection. Cost Analysis and Budget Considerations The financial aspect of installing and maintaining above ground storage tanks is a significant consideration. When it comes to upfront costs, single wall tanks generally have a lower initial cost compared to double wall tanks. This can make them an attractive option for businesses operating on a tight budget. However, it is crucial to also consider the long-term costs associated with each type of tank. For single wall tanks, additional expenses may be incurred for secondary containment systems, such as concrete structures or other approved methods. These costs can add up over time, potentially offsetting the initial cost savings [3, 4]. Furthermore, if a leak occurs and the secondary containment fails, the cost of clean-up and potential fines for environmental damage can be substantial. Double wall tanks, on the other hand, come with a higher initial cost. However, their built-in secondary containment eliminates the need for additional containment measures, potentially saving costs in the long run [3, 4]. Furthermore, in the event of a leak, the secondary containment can prevent the leaked substance from entering the environment, potentially saving on clean-up costs and avoiding fines. Therefore, when considering the cost of single wall vs. double wall tanks, it's important to look beyond the initial investment. A comprehensive cost analysis should include both upfront and long-term costs, including potential clean-up costs and fines in case of leaks. This will provide a more accurate picture of the total cost of ownership, enabling an informed decision to be made. Environmental Impact and Sustainability The decision between single wall and double wall tanks can have significant implications for the environment. Single wall tanks, if not equipped with effective secondary containment, carry a higher risk of environmental damage in the event of a leak. This can lead to soil and water contamination, which can have serious consequences for local ecosystems and public health. On the other hand, double wall tanks, with their built-in secondary containment, provide an added layer of protection, minimizing the potential for environmental contamination. In the event of a leak, the secondary containment layer acts as a barrier, preventing the leaked substance from escaping into the environment. By choosing double wall tanks, businesses can demonstrate their commitment to environmental stewardship. These tanks offer a higher level of safety and reduce the risk of environmental damage, contributing to the long-term sustainability of operations. This can enhance a business's reputation as an environmentally responsible entity and can potentially contribute to customer trust and loyalty. Moreover, as environmental regulations become more stringent and public awareness of environmental issues increases, the use of double wall tanks can help businesses stay ahead of the curve. By investing in double wall tanks, businesses can not only meet current regulations but also be prepared for potential future regulatory changes aimed at further protecting the environment. Real-World Examples and Recommendations In a real-world example discussed on the AST Forum, a 290-gallon steel AST used for storing and dispensing gasoline raises questions about determining if the tank is single wall or double wall just by observing the vents. In this case, without visible markings or labels to provide information about the tank's construction, it can be challenging to determine if the tank is single or double-walled. One recommendation in such situations is to consult the manufacturer's specifications or seek professional advice. Visual indicators, such as a slightly larger size, a vacuum gauge to monitor the vacuum between the layers, and the absence of a separate epoxy-coated concrete structure, may suggest a double wall tank. However, these indicators are not foolproof, and it is always best to seek professional advice or consult the manufacturer's specifications to confirm the type of tank. In addition to observing the physical characteristics of the tank, regular inspections and maintenance can also provide insights into the tank's construction. For instance, during maintenance, the presence of a secondary containment layer or a leak detection system may indicate a double wall tank. Therefore, regular inspections and maintenance are not only important for ensuring the safe operation of the tank but can also provide valuable insights into its construction. Maintenance and Longevity of Tanks The maintenance of above ground storage tanks is crucial for ensuring their longevity and safe operation. Regular inspections, leak monitoring, and adherence to maintenance guidelines provided by the manufacturer are key aspects of tank maintenance, regardless of whether they are single wall or double wall tanks. For single wall tanks, regular inspections of the tank and the secondary containment structure are essential. Any signs of wear or damage should be promptly addressed to prevent leaks and environmental contamination. Regular maintenance also includes checking for signs of corrosion, which can compromise the integrity of the tank and lead to leaks. For double wall tanks, both the primary and secondary containment layers should be regularly inspected for signs of corrosion or leaks. The monitoring systems, if present, should be tested and calibrated to ensure accurate detection of any leaks. While the built-in secondary containment of double wall tanks provides an added layer of protection, it does not eliminate the need for regular inspections and maintenance. With proper maintenance, both single and double wall tanks can provide long-term reliability and cost-effectiveness. In fact, with proper maintenance, double-wall oil tanks can last up to 50 years. This underlines the importance of regular inspections and maintenance in ensuring the longevity of above ground storage tanks. Future Trends and Innovations in Tank Design The field of above ground storage tanks is continually evolving, with ongoing advancements in materials, design, and technology. Future trends and innovations may include improved corrosion-resistant materials, enhanced leak detection systems, and more sustainable and environmentally-friendly designs. For example, advancements in material technology can lead to the development of more corrosion-resistant materials, enhancing the longevity and durability of above ground storage tanks. Improved leak detection systems, capable of detecting even the smallest leaks in real-time, can provide early warning of potential issues, allowing for prompt action to prevent environmental damage. Sustainable and environmentally-friendly designs are another potential area of innovation. As environmental regulations become more stringent and public awareness of environmental issues increases, the demand for sustainable and environmentally-friendly storage solutions is likely to grow. This could lead to the development of tanks made from recycled or eco-friendly materials, or designs that minimize the risk of leaks and environmental contamination. As technology continues to evolve, it is essential to stay updated on the latest innovations and trends in tank design and technology. By embracing new technologies and sustainable practices, businesses can ensure the safe and efficient storage of substances while minimizing their environmental footprint and meeting regulatory requirements.
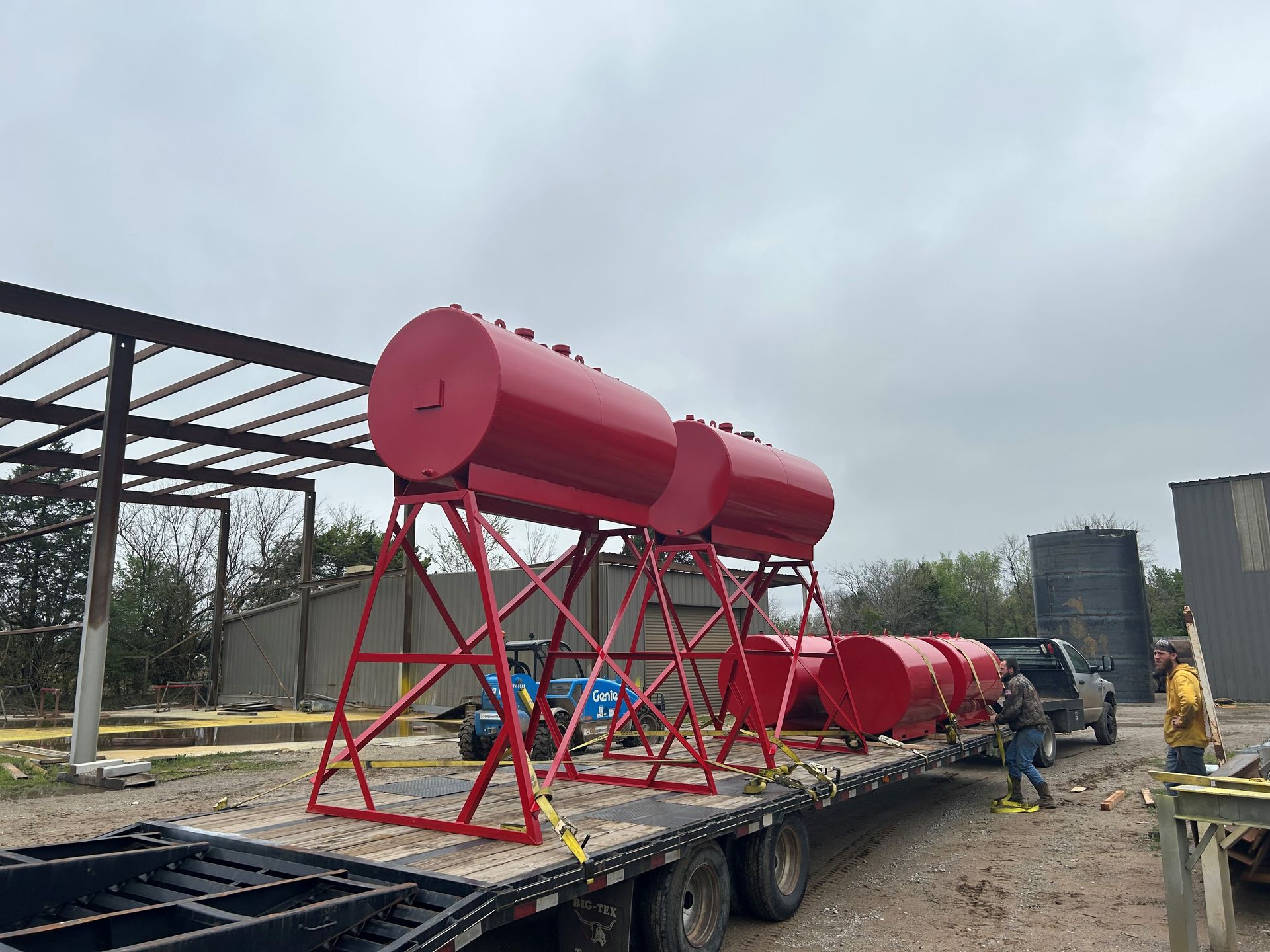
In an ever-evolving energy landscape, the role of above-ground fuel storage technology is becoming increasingly critical. Innovations in the field are creating more efficient, secure, and environmentally friendly fuel storage solutions. From cutting-edge construction techniques to advanced monitoring systems, these innovations are transforming the way fuel is stored and used. This article delves into the latest advancements in above-ground fuel storage technology and their implications for various industries. Innovations in Industrial Storage Tanks: Internal Floating Roofs Industrial storage tanks are witnessing continuous advancements with the integration of state-of-the-art features and technologies. One such innovation is the introduction of internal floating roofs, specifically designed for storing large quantities of crude oil and other petroleum products. These roofs, by floating on the surface of the stored liquid, minimize the vapor space and therefore, substantially reduce the risk of vapor release and emissions. For instance, in a large-scale oil storage facility, internal floating roofs can significantly curb the emissions of volatile organic compounds (VOCs) by up to 95% compared to traditional fixed roofs. This helps companies comply with environmental regulations while also contributing to a cleaner and safer working environment. Enhanced Safety with Secondary Containment Systems and Polyethylene Lining Another important innovation in the construction of above-ground fuel storage tanks is the use of secondary containment systems or double-walled tanks. These systems offer an extra layer of protection against leaks and spills by safeguarding the main storage vessel. In the event of a leak from the primary tank, the secondary containment system prevents the leaked substance from infiltrating the environment. This helps companies avoid expensive cleanup operations and potential legal liabilities. Moreover, the implementation of polyethylene lining on steel tanks is another notable innovation. This lining acts as a defensive shield against corrosive activities, thus preventing structural damage. Further, molecular bonding techniques are being employed to strengthen the tanks and enhance their durability. These advancements in construction techniques, combined with regular inspection and maintenance, ensure the longevity and integrity of above-ground fuel storage tanks. Material Selection: Ensuring Durability and Corrosion Resistance In the construction of above-ground fuel storage tanks, the selection of materials plays a pivotal role in ensuring durability and preventing corrosion. Polyethylene lining on steel tanks is a key feature that safeguards against corrosive activities and structural damage. This lining serves as a protective barrier, enhancing the longevity of the tanks. Another material of significance is Inconel 625, a high-strength nickel-based alloy, often chosen as the preferred metal for the primary membrane due to its compatibility with fuel oil. This alloy exhibits excellent corrosion resistance and high strength at high temperatures, making it ideal for use in fuel storage tanks. By using these materials, companies can prevent leaks, corrosion, and structural failures, ensuring the safe storage of fuel and minimizing the risk of environmental contamination. Advanced Monitoring and Leak Detection Systems in Modern Fuel Storage Tanks Modern fuel storage tanks are equipped with advanced monitoring and leak detection systems, providing real-time information on fuel levels, pressure, and temperature. These systems enable operators to keep a close eye on the storage conditions and quickly detect any abnormalities or potential leaks. For example, a dual membrane system with a repurposed interbarrier space allows for effective leak detection. By monitoring the interbarrier space for any changes in pressure or gas composition, operators can quickly identify and address potential leaks. Moreover, the use of pre-assembled components into panels also facilitates installation, especially in tanks with limited access dimensions. This modular approach to construction allows for rapid installation and reduced downtime, improving operational efficiency. Revolutionizing Fuel Dispensing with Modern Technology The advancements in fuel dispensing technology have also been significant, revolutionizing the way fuel is delivered. Modern fuel dispensing systems allow for efficient and accurate fuel delivery, ensuring that the right amount of fuel is dispensed every time. These systems are automated and equipped with precise measurement capabilities, ensuring controlled and safe fuel dispensing and minimizing the risk of spills or overfilling. For instance, some fuel dispensing systems are equipped with automatic shut-off valves that prevent fuel from being dispensed if a vehicle's tank is full. This not only prevents fuel wastage but also reduces the risk of fuel spills and environmental contamination. Moreover, these systems are compatible with a variety of fuel types and feature advanced nozzle designs that enhance the fueling process. By implementing these advanced fuel dispensing systems, companies can improve efficiency, enhance safety, and minimize environmental impact. Above-Ground Fuel Storage Applications in Various Industries The implementation of above-ground fuel storage technologies varies across industries, reflecting the diverse needs and challenges of different sectors. For instance, the U.S. Navy emphasizes careful attention to fuel delivery, storage, and distribution to avoid adverse environmental impacts. They prioritize the use of innovative concepts and technologies to ensure safe and efficient fuel storage. One example is the use of fuel bladders, flexible containers that can be easily transported and deployed in remote locations. These bladders provide a temporary storage solution for fuels, enabling the Navy to operate in areas where permanent storage infrastructure is not available. Such innovations demonstrate the adaptability of above-ground fuel storage technology and its potential to address diverse storage needs. Advanced Storage Technologies in the Nuclear Industry In the nuclear industry, the use of advanced storage technologies is crucial for managing used nuclear fuel. Holtec International's HI-STORM system, for instance, is utilized for the dry storage of used nuclear fuel. This system features interchangeable sealed metallic Multi-Purpose Canisters (MPCs), a vertically ventilated storage overpack, or underground Vertical Ventilated Module (VVM), and an on-site transfer cask known as HI-TRAC. The HI-STORM system is designed with safety and logistical benefits in mind, complying with environmental standards and ensuring the safe and secure storage of nuclear fuel. The implementation of advanced above-ground fuel storage technologies in the nuclear industry underscores the potential of these innovations to address complex storage needs and contribute to safe and sustainable energy practices. Environmental Considerations in Above-Ground Fuel Storage Systems Environmental considerations and regulations play a crucial role in shaping the design and operation of above-ground fuel storage systems. Stringent environmental regulations govern above-ground fuel storage to minimize potential risks and protect the environment. Companies must adhere to these regulations and implement best practices to prevent environmental contamination. Proper maintenance and regular inspection procedures are crucial to ensure compliance with these regulations. For example, advanced leak detection systems are extensively used to prevent potential environmental contamination. These systems enable early detection of leaks, allowing for prompt remedial action and minimizing the impact on the surrounding environment. By complying with environmental regulations and implementing advanced leak detection systems, companies can demonstrate their commitment to environmental sustainability and responsible fuel storage practices. Benefits of Above-Ground Fuel Storage Over Other Options Above ground fuel storage offers several benefits over other storage options. Firstly, it provides ease of installation and accessibility for maintenance. With above-ground tanks, installation can be completed more quickly and maintenance tasks can be performed more easily compared to underground tanks. This means that tanks can be easily installed and inspected, reducing downtime and maximizing operational efficiency. Secondly, above-ground storage allows for cost-effective expansion and modification. Unlike underground storage options, companies can easily increase the storage capacity or implement additional features, such as secondary containment systems, to meet their changing needs. This flexibility makes above-ground storage a cost-effective option for many companies. Operational Advantages of Above-Ground Fuel Storage Tanks Furthermore, above-ground storage tanks provide better visibility and control during fueling operations, enhancing safety and efficiency. Operators can easily monitor the fuel levels and quickly identify any issues, ensuring a smooth and controlled fueling process. Additionally, above-ground tanks are designed to withstand various weather conditions, ensuring the uninterrupted supply of fuel. This reliability, combined with the increased capacity of modern tanks, makes above-ground storage a preferred option for many businesses. By choosing above-ground storage, companies can achieve operational efficiency, reduce costs, and ensure the safe and secure storage of fuel. Enhanced Performance Features in Modern Industrial Storage Tanks Modern industrial storage tanks come with advanced features that further enhance their performance. For instance, internal floating roofs minimize the vapor space, reducing the risk of evaporation and emissions. This not only helps companies comply with environmental regulations but also contributes to a cleaner and safer working environment. Secondary containment systems provide an extra layer of protection against leaks and spills, ensuring the safety and integrity of the main storage vessel. Thermally insulated above-ground storage tanks are designed to maintain high mechanical strength and integrity, even in extreme temperatures. These advanced features ensure the safe and efficient storage of fuel, minimizing the risk of environmental contamination and ensuring operational reliability. Advancements in Natural Gas Storage Technologies While the focus of this article is on above-ground fuel storage, it is worth mentioning that natural gas storage technologies are also witnessing significant advancements. Adsorbed Natural Gas Storage (ANGS) utilizes activated carbon to store natural gas at high pressures, increasing storage capacity and reducing infrastructure costs. Cryogenic Natural Gas Storage involves cooling natural gas to a liquid form, enabling higher storage density and global trade opportunities. Underground natural gas storage utilizes depleted fields or caverns, providing seasonal storage, enhanced system reliability, and reduced price volatility. These innovative natural gas storage technologies play a crucial role in meeting the growing demand for clean and sustainable energy sources. Efficiency and Safety Improvements in Natural Gas Storage Technological advances in natural gas storage continue to improve efficiency and safety. For example, advancements in underground storage, Compressed Natural Gas (CNG) storage materials, and nanotechnology play a crucial role in enhancing the performance of natural gas storage systems. Cryogenic energy storage and CNG storage offer cost-effective and cleaner alternatives for transportation fuel. Continued research and innovation in natural gas storage technologies are crucial for sustainability and efficiency in the industry. By developing more efficient and reliable natural gas storage systems, companies can contribute to a greener and more sustainable energy future. The Promising Future of Above-Ground Fuel Storage Technology Looking ahead, the future of above-ground fuel storage technology is promising. Further advancements in underground storage will enhance capacity and operational efficiency. The expansion of Compressed Natural Gas (CNG) and Liquefied Natural Gas (LNG) infrastructure will facilitate the widespread adoption of natural gas as a cleaner fuel source. Integration with renewable energy sources will contribute to a more sustainable and diversified energy mix. Ongoing research and development in above-ground fuel storage technology will continue to drive innovation, shaping the future of the industry. By investing in the development of advanced above-ground fuel storage technologies, companies can position themselves at the forefront of the energy industry and contribute to a more sustainable and efficient energy future. The Significance of Innovations in Fuel Storage Technology In conclusion, the latest innovations in above-ground fuel storage technology offer improved safety, efficiency, and environmental compliance. These advancements in construction techniques, materials, monitoring systems, and fuel dispensing technology enhance the storage and distribution of fuel. By implementing these technologies, companies can ensure the safe and efficient storage of fuel, minimize the risk of environmental contamination, and comply with stringent regulations. With ongoing research and development, the future of above-ground fuel storage technology looks promising, paving the way for a more sustainable and efficient energy industry. These advancements underline the importance of continuous innovation in fuel storage technology and the need for businesses to stay abreast of these trends to remain competitive and sustainable in the long term.
Learn about UL-certified aboveground storage tanks, designed for safely storing flammable and combustible liquids. Understand the significance of the UL 142 certification and its stringent safety standards. Discover the key features, construction requirements, and various certifications like UL 80 and UL-2085 that cater to different storage needs and offer enhanced safety measures.