Metal Fabrication Trends 2023: Shaping the Future
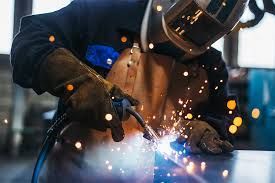
Metal fabrication has always been a cornerstone of industrial development, providing the backbone for countless industries from automotive to aerospace. As technology advances, so does the demand for more precise, efficient, and sustainable metal fabrication processes. In 2023, the metal fabrication industry is witnessing transformative trends that are not only shaping the present but also setting the course for future innovation. In this blog, we’ll explore the key trends in metal fabrication that are revolutionizing the industry this year and beyond.
1. Automation and Robotics: The Rise of the Smart Factory
Automation is no longer just a buzzword; it's an integral part of the future of metal fabrication. With labor shortages, the need for greater efficiency, and the pressure to maintain competitive pricing, automation is stepping in to bridge the gap. Robots and automated systems are taking over repetitive tasks such as welding, cutting, and assembly, freeing up skilled labor for more complex jobs.
Collaborative robots, also known as cobots, are designed to work alongside human operators. They improve productivity while maintaining flexibility, allowing manufacturers to scale operations without the need for massive workforce expansion. In 2023, we see a surge in factories implementing these smart technologies, leading to faster production times, fewer errors, and lower costs.
What to Expect: The integration of artificial intelligence (AI) with automation systems is driving real-time decision-making and predictive maintenance. This reduces downtime and ensures that machinery operates at optimal efficiency. Companies that embrace this trend are more likely to stay ahead of the competition in terms of quality, precision, and speed.
2. Sustainability and Eco-Friendly Practices: A Green Revolution
Sustainability is no longer optional; it's a necessity. The metal fabrication industry is under increasing pressure to reduce its carbon footprint and adopt eco-friendly practices. In 2023, more metal fabricators are turning to green manufacturing methods, including recycling scrap metal, using sustainable materials, and adopting energy-efficient production processes.
The push for sustainability is also influencing the design of products. Lightweight materials that reduce energy consumption during transportation and use are becoming more popular, especially in industries like automotive and aerospace. Additionally, reducing waste and optimizing resource use have become key areas of focus for companies looking to stay competitive while minimizing their environmental impact.
What to Expect: Sustainability in metal fabrication is driven by innovation. From the adoption of renewable energy sources in factories to the use of advanced software for waste reduction, the future of metal fabrication is green. Fabricators that implement these practices are likely to benefit from both cost savings and enhanced reputation, especially as consumer awareness around sustainability grows.
3. Additive Manufacturing: Beyond Prototyping
Additive manufacturing, commonly known as 3D printing, is not new to metal fabrication, but in 2023 it is reaching new heights. While initially limited to prototyping, 3D printing has evolved into a technology capable of producing fully functional metal parts with complex geometries that traditional manufacturing methods cannot achieve.
One of the significant advantages of additive manufacturing is its ability to produce parts on demand, reducing the need for large inventories and minimizing lead times. In industries where customization and small batch production are essential, such as aerospace and medical devices, additive manufacturing is proving to be a game-changer.
What to Expect: As the technology becomes more advanced and accessible, we can expect to see even greater adoption of 3D printing in metal fabrication. The future lies in hybrid manufacturing processes that combine traditional methods with additive techniques, offering the best of both worlds in terms of speed, precision, and versatility.
4. Digitalization and Industry 4.0: Smart Metal Fabrication
The rise of Industry 4.0 is revolutionizing how metal fabricators operate. By embracing digital technologies such as the Internet of Things (IoT), cloud computing, and advanced data analytics, manufacturers are creating smart factories that can monitor, control, and optimize every aspect of production in real time.
In 2023, digital twins—virtual replicas of physical machines and processes—are being used to simulate and optimize production lines before making changes in the real world. This reduces downtime and ensures that equipment operates at peak efficiency. Additionally, advanced sensors embedded in machinery provide continuous feedback, enabling predictive maintenance that prevents costly breakdowns.
What to Expect: The trend towards digitalization is set to continue, with more metal fabricators leveraging big data and AI to improve decision-making, reduce waste, and enhance product quality. Those who fail to adopt Industry 4.0 technologies risk falling behind their competitors.
5. Advanced Materials: Strength Meets Lightweight Design
Material science is playing an increasingly important role in metal fabrication, especially as industries such as automotive, aerospace, and defense seek stronger yet lighter materials. In 2023, the demand for advanced materials, such as high-strength steel, aluminum alloys, and titanium, continues to grow. These materials offer exceptional durability and performance while reducing weight, which is crucial for fuel efficiency and sustainability.
Metal fabricators are also exploring new composite materials that combine metal with other substances, such as carbon fiber, to create components that are not only strong and lightweight but also resistant to corrosion and wear.
What to Expect: The development of new materials will continue to drive innovation in metal fabrication. As industries push for greater performance and sustainability, fabricators must stay up to date with the latest advancements in material science to meet these evolving demands.
6. Cybersecurity: Protecting the Future of Metal Fabrication
As metal fabrication becomes more digital and connected, the need for robust cybersecurity measures is greater than ever. Smart factories that rely on IoT devices, cloud-based systems, and data analytics are vulnerable to cyberattacks. In 2023, cybersecurity is a top concern for metal fabricators looking to protect their sensitive information, intellectual property, and operational systems.
Cybersecurity threats can result in production downtime, data breaches, and financial losses. Therefore, metal fabricators are increasingly investing in secure networks, encrypted communications, and advanced firewalls to safeguard their operations.
What to Expect: Cybersecurity will remain a critical focus for metal fabricators as they adopt more digital technologies. Companies that prioritize cybersecurity can prevent costly disruptions and ensure the integrity of their operations.
7. Customization and On-Demand Manufacturing
In an era where customers demand personalized products, metal fabricators are adapting by offering more customization options and on-demand manufacturing services. Thanks to advancements in software and machinery, fabricators can now produce bespoke metal components in small batches with minimal setup time.
This trend is particularly relevant in industries like consumer electronics, medical devices, and automotive, where customization can set a company apart from its competitors. In 2023, metal fabricators are focusing on flexibility and responsiveness, allowing them to meet the unique needs of their clients without sacrificing efficiency.
What to Expect: Customization will continue to be a driving force in metal fabrication. As consumer expectations evolve, metal fabricators must stay agile, offering tailored solutions that cater to the individual needs of their clients.
Conclusion
The metal fabrication industry is at the forefront of innovation, with 2023 ushering in transformative trends that will shape its future. From automation and sustainability to advanced materials and digitalization, metal fabricators are embracing new technologies and practices that improve efficiency, reduce costs, and enhance product quality. Companies that stay ahead of these trends will be better equipped to meet the evolving demands of their clients and remain competitive in the global market.
At Weldco Manufacturing, we are committed to staying at the cutting edge of the metal fabrication industry. Our team of experts is dedicated to delivering high-quality, precision-engineered metal products that meet the unique needs of our clients. Whether you need custom metal fabrication, advanced materials, or sustainable manufacturing solutions, we’ve got you covered. Visit weldcomfg.com to learn more about our services and how we can help shape your future.